Гибка на растяжение профилей из листового металла и алюминия
Процесс формирования растяжки
Формование растяжением/гибка может использоваться для создания различных форм, включая плавные изгибы, сложные изгибы и даже острые углы. Это делает его идеальным для создания конструктивных элементов с точными размерами и контурами, которые можно использовать с различными металлами, включая алюминий, сталь и титан.
В этой статье содержится вся информация, которую вам нужно знать о формировании растяжек. Читайте дальше и узнайте больше о:
Ниже вы узнаете:
- Что такое стретч-формование?
- Терминология, используемая при стретч-формовании
- Механика стретч-формования
- Виды стретч-формования
- И многое другое…
Что такое формирование растяжки?
Формовка с растяжением (также называемая гибкой с растяжением) — это процесс обработки металла, который включает растягивание листа или металлической детали через матрицу для создания сложных контурных форм. Он широко используется в аэрокосмической, автомобильной и архитектурной промышленности для изготовления деталей точной формы с жесткими допусками.
Процесс начинается с плоского листа или металлической профильной детали (обычно алюминиевых профилей), которая зажимается по краям и закрепляется на месте. Затем материал подвергается растягивающему усилию, которое натягивает его на матрицу или формовочный блок. Этот процесс растяжения приводит к деформации материала и принятию формы матрицы. Формование с растяжением может выполняться при комнатной температуре, что устраняет необходимость в высокотемпературных процессах, таких как горячее формование.

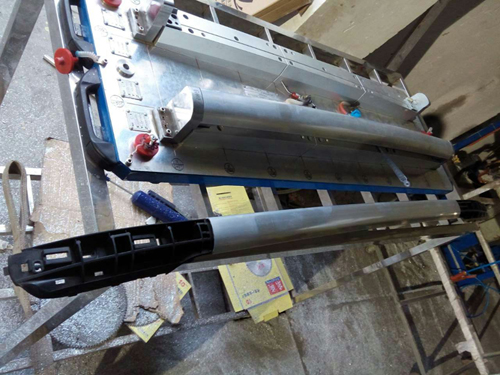


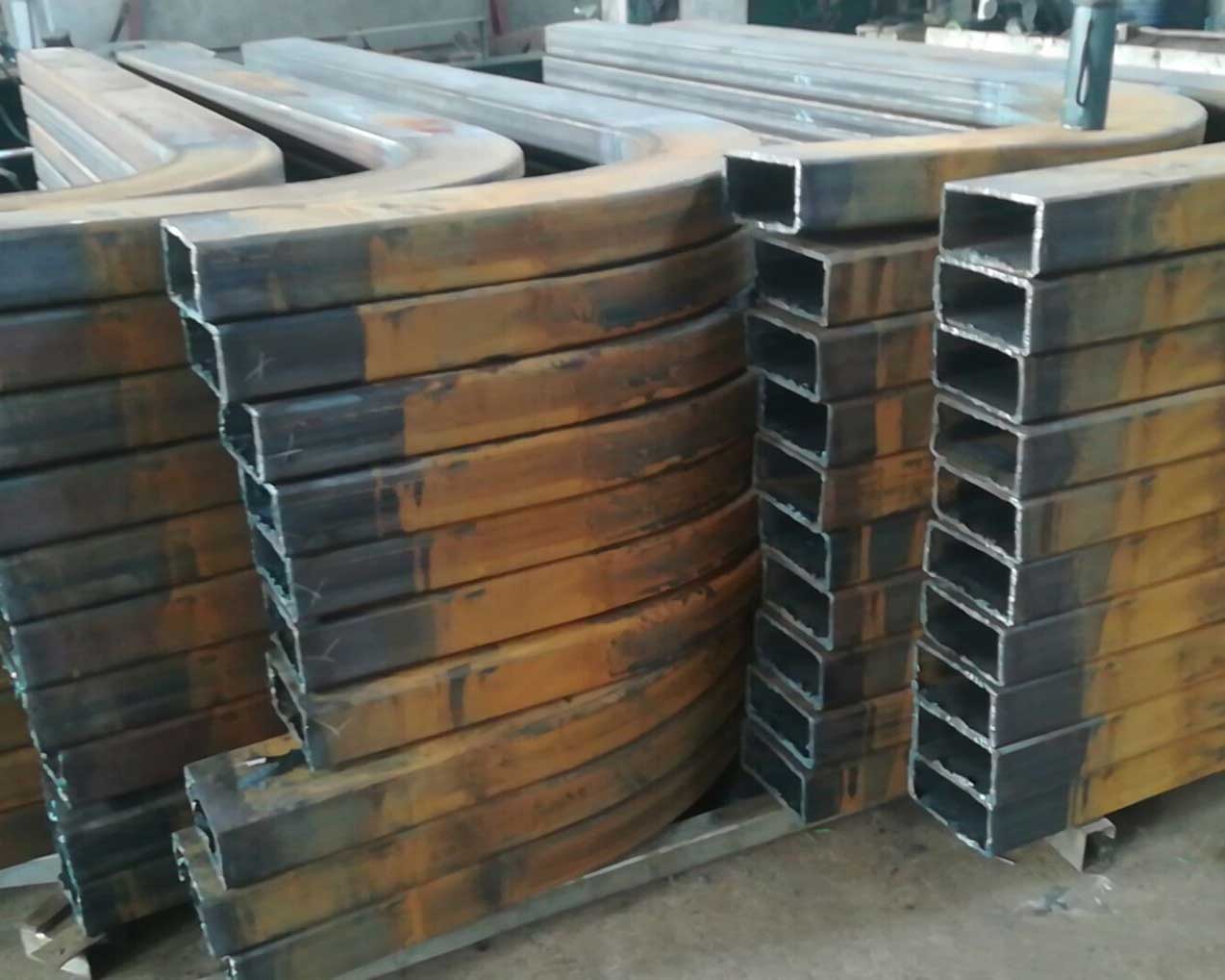

Одним из ключевых преимуществ формования методом растяжения является его способность создавать сложные трехмерные формы с высокой степенью точности и повторяемости. Это особенно полезно для изготовления криволинейных деталей, таких как секции фюзеляжа самолета, панели кузова автомобиля и архитектурные компоненты, такие как изогнутые фасады.
Формовка методом растяжения обладает рядом преимуществ, в том числе сокращением отходов материала, поскольку сводит к минимуму необходимость в резке и сварке, а также позволяет изготавливать детали с гладкой и однородной поверхностью. Кроме того, он может работать с широким спектром материалов, включая алюминий, сталь и титан.
Топ-7 преимуществ растягивающегося формования
Процесс формования с растяжением обладает рядом преимуществ по сравнению с гибкой в рулонах, особенно при формировании больших полых профилей, обеспечивая при этом сохранение целостности поверхности. Формование с растяжением хорошо подходит для проектов, требующих больших радиусов, специальных изгибов и даже 3D-формования.
- Обработка больших полых профилей: Формовочная машина Stretch отлично подходит для гибки больших полых профилей или секций. Она способна выдерживать значительные размеры таких материалов, что делает ее идеальной для применения в строительстве, архитектуре и других отраслях промышленности, где используются крупногабаритные конструкции.
- Сохранение целостности поверхности: Формовка при растяжении сводит к минимуму риск повреждения поверхности или дефектов в процессе гибки. Это особенно важно при работе с материалами, требующими гладкой и неповрежденной поверхности, такими как алюминий или нержавеющая сталь, используемые в архитектурных элементах.
- Меньшие радиусы: При формовании методом растяжения можно получить меньшие радиусы изгиба по сравнению с гибкой в рулоне. Это важно для проектов, требующих точности кривизны материалов, например, в автомобильной и аэрокосмической промышленности, где для гибки труб и компонентов требуются меньшие радиусы.
- Специальные изгибы: Гибкость формования при растяжении позволяет создавать специальные изгибы и нестандартную геометрию. Он хорошо подходит для применений, где стандартные радиусы изгиба не соответствуют конкретным требованиям проекта, например, в художественном или архитектурном дизайне.
- 3D-гибка: Растягивающая формовка способна создавать трехмерные изгибы, позволяя создавать сложные формы. Это особенно ценно в отраслях, где распространены уникальные и нестандартные конструкции, например, в художественных инсталляциях, скульптуре или сложных архитектурных элементах.
- Возможности: Гибка с растяжением особенно эффективна при формировании сложных трехмерных форм с высокой степенью точности. Она может обрабатывать узкие изгибы и формы с различными радиусами вдоль изгиба.
- Материалы: Он может работать с различными материалами, включая металлы, такие как алюминий, сталь и титан.
- Точность: Гибка при растяжении обеспечивает точность и может соответствовать жестким допускам. Он идеально подходит для применений, где точность размеров имеет решающее значение.
Многосторонность
Растягивающее формование можно использовать для создания самых разнообразных форм и геометрий, от простых изгибов до сложных кривых и острых углов.
- Разнообразие материалов: Его можно применять к широкому спектру материалов, включая металлы, такие как алюминий, сталь и нержавеющая сталь, а также пластмассы, что обеспечивает гибкость в выборе материала в зависимости от конкретных требований.
- Сложные формы: Формование методом растяжения позволяет создавать замысловатые формы, что делает его пригодным для производства широкого спектра компонентов с различной геометрией.
- Различные отрасли промышленности: Его адаптивность распространяется на все отрасли, включая аэрокосмическую, автомобильную, архитектурную и морскую, демонстрируя его универсальность в удовлетворении потребностей различных секторов.
- Переменные размеры: Формование растяжением применимо как к мелким, так и к крупным деталям, обеспечивая широкий диапазон размеров, от небольших сложных деталей до крупных конструктивных элементов.
- Оно позволяет осуществлять гибку растяжением профилей с несколькими дугообразными сегментами и переменной кривизной.
- Точность изгиба дуги высока, отскок материала стабилен, а размер заготовки постоянен.
- Это позволяет эффективно устранить остаточное напряжение внутри материала, и изделие обладает хорошей стабильностью размеров.
- Благодаря холодному упрочнению металлических материалов механические свойства материала могут быть улучшены после растяжения и гибки.
Точность
Формование методом растяжения позволяет получать высокоточные и однородные формы, что делает его идеальным для применения с высокими допусками.
- Высокая точность: При формовании методом растяжения достигается исключительная точность размеров, гарантирующая точное соответствие формованных деталей проектным спецификациям.
- Жесткие допуски: Процесс может постоянно соответствовать жестким допускам, что крайне важно в таких отраслях, как аэрокосмическая и автомобильная, где точность имеет первостепенное значение.
- Однородность: Формовка растяжением позволяет получать детали одинаковой формы и размеров на всех этапах производства, сводя к минимуму вариации и обеспечивая взаимозаменяемость деталей. Равномерная толщина стенок: Формовка растяжением помогает поддерживать равномерную толщину стенок материала, обеспечивая структурную целостность и стабильное качество продукции.
- Минимальное образование складок и деформаций: Этот процесс сводит к минимуму образование складок и деформаций материала, в результате чего получаются гладкие и эстетически приятные готовые изделия.
- Повышенная прочность материала: Растягивающее формование может улучшить механические свойства некоторых материалов, делая их прочнее и долговечнее.
- Минимальное искажение материала: Растягивающее формование сводит к минимуму искажение материала, сохраняя целостность формованных деталей и уменьшая необходимость в последующей обработке.
- Высокое качество поверхности: В результате этого процесса получаются детали с высококачественной отделкой поверхности, устраняющей необходимость в дополнительной обработке поверхности или повторной полировке.
- Воспроизводимость: Повторяемость процесса формования при растяжении гарантирует, что идентичные детали могут изготавливаться последовательно, сохраняя стандарты качества и производительности.
Эффективность
Формование с растяжением позволяет получать сложные формы за один этап, что сокращает необходимость в многократных операциях формования.
- Экономия материалов: Процесс сводит к минимуму потери материала за счет растяжения и придания формы материалу именно там, где это необходимо, снижая общий расход материала и стоимость.
- Быстрое производство: Формование с растяжением позволяет эффективно изготавливать детали, поскольку часто требует меньшего количества производственных этапов, смены инструмента и последующей обработки по сравнению с альтернативными методами формования.
- Высокая производительность: Он хорошо подходит для крупносерийного производства благодаря своей эффективности и потенциалу для непрерывных автоматизированных операций.
- Адаптивность оснастки: При формовании методом растяжения можно использовать различные настройки оснастки, что позволяет быстро адаптироваться к изменяющимся требованиям к деталям без значительных изменений оснастки.
- Минимальная последующая обработка: Точность, достигаемая при формовании методом растяжения, часто устраняет необходимость в обширной последующей обработке, что еще больше оптимизирует производство и сокращает трудозатраты и временные затраты.
- Гарантия качества: Последовательность процесса гарантирует, что каждая деталь соответствует проектным требованиям, что сокращает необходимость в проверке и доработке.
- Экономичность: Оптимизируя использование материалов, сокращая количество отходов и повышая эффективность производства, stretch forming предлагает экономичные решения для отраслей промышленности, требующих высокоточных компонентов.
Сила
В результате формования при растяжении получается материал с более высокой прочностью и долговечностью, чем при других процессах формования.
- Улучшенные свойства материалов: Формование с растягиванием может улучшить механические свойства материалов, такие как повышение прочности на растяжение и уменьшение слабых мест материала.
- Структурная целостность: Это позволяет создавать компоненты с превосходной структурной целостностью, гарантируя, что формованные детали могут выдерживать механические нагрузки и сохранять свою форму под нагрузкой.
- Равномерная толщина: Растягивающее формование помогает поддерживать равномерную толщину материала по всей детали, способствуя постоянной прочности и долговечности.
- Подходит для конструктивных элементов: В таких отраслях промышленности, как аэрокосмическая и автомобильная, где прочность имеет решающее значение, для изготовления прочных конструктивных элементов предпочтительно растягивающее формование.
7 минусов процесса формирования растяжки
- Ограничение по размеру поперечного сечения: Размер и форма деталей, которые могут быть сформованы методом растяжения, ограничены тоннажем оборудования и размером зажимов.
- Высокие инвестиционные затраты на оснастку: Изготовленные на заказ формы и оснастка для формования методом растяжения могут быть дорогостоящими, особенно по сравнению с другими процессами обработки металлов давлением.
- Ограниченная универсальность пресс-форм: Формы для формования методом растяжения часто разрабатываются для конкретных применений, что ограничивает их адаптируемость.
- Проблемы с асимметричными профилями: При работе с асимметричными профилями формирование на растяжку может быть проблематичным.
- Затраты на материалы и энергию: Процесс растяжения требует значительных усилий и энергии, что приводит к увеличению эксплуатационных расходов. Потери материалов, особенно при использовании дорогих или редких материалов, могут вызывать беспокойство.
- Ограничения при формировании резких контуров и возвращающихся углов: Формообразование растяжением плохо подходит для деталей с резкими контурами или возвращающимися углами, что делает его менее подходящим для сложных геометрических форм.
- Невозможность исправить неровности поверхности: Без защемления между сопрягаемыми матрицами нет возможности исправить незначительные неровности поверхности материала, что потенциально может привести к дефектам конечного продукта.
Принцип работы
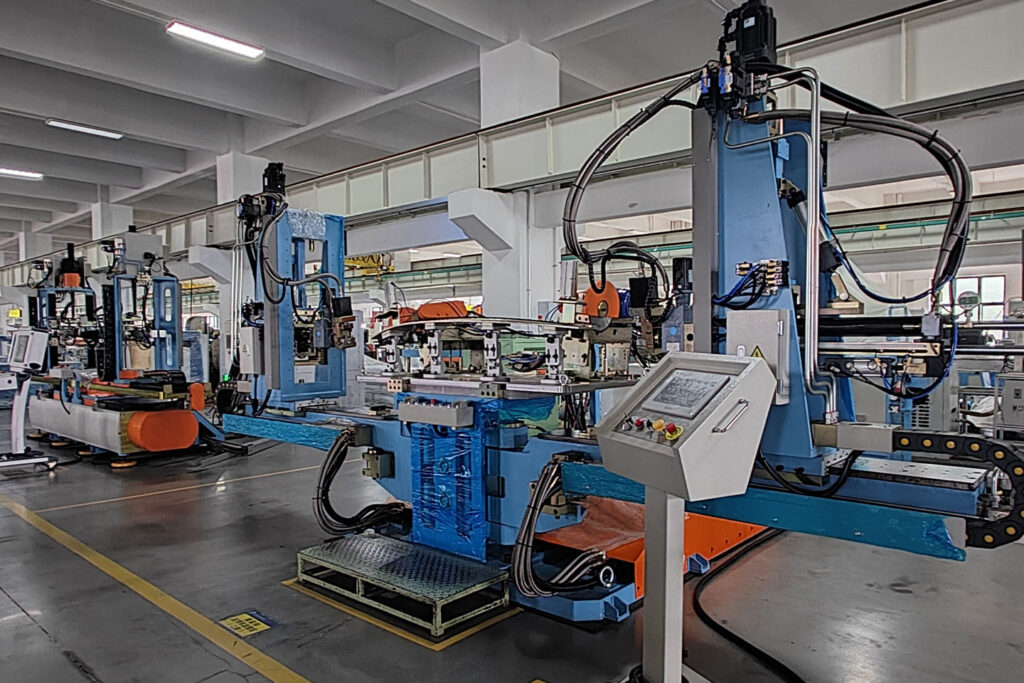
Растягивающее формование — очень сложный процесс, требующий высокой точности.
Если бы деталь была изогнута без предварительного растяжения, во время процесса возникли бы две естественные силы. Во-первых, одна половина детали естественным образом растянулась бы. Во-вторых, другая половина подверглась бы сжатию, и нейтральная ось была бы разделением между ними. Растяжение материала компенсирует сжатие, которое обычно происходит на внутренней поверхности детали, что, в свою очередь, устраняет образование складок или скручивание. Можно сказать, что машина для формования на растяжку сгибает детали в криволинейные формы, но делает это, одновременно вытягивая складки из детали до того, как они успеют образоваться.
При таком сочетании изгиба и растяжения наружные волокна формуемой детали испытывают растяжение при растяжении, достаточное для того, чтобы привести это волокно к текучести, т.е. оно было растянуто сверх своей способности вернуться к своей первоначальной длине после ослабления растягивающего усилия. Таким образом, детали остаются близкими к форме формовочного блока после его извлечения из машины для формования на растяжку.
Растягивающее действие, происходящее в процессе формования при растяжении, не только устраняет образование складок, но и помогает устранить “пружинистость” детали, отклоняющуюся от желаемого готового контура. Несмотря на то, что это холодная форма гибки, в процесс формования при растяжении может быть введено тепло, позволяющее изгибать экзотические сплавы.
14 Терминология для формирования растяжек
- Матрица: Инструмент или пресс-форма, используемые при формовании с растяжением, которые определяют конечную форму, которую примет металл. Матрицы обычно изготавливаются на заказ в соответствии с конкретной геометрией формуемой детали.
- Усилие растяжения: усилие, прикладываемое к металлическому листу или детали для растягивания его через матрицу.
- Радиус изгиба: радиус кривизны, которого достигнет металлический лист или деталь при формовании на растяжку. Это важный параметр для определения желаемой формы.
- Растяжение: Состояние напряжения в металле, при котором он растягивается во время процесса. Растяжение является критическим фактором для достижения желаемой формы без разрушения материала.
- Сжатие: Состояние напряжения в металле, при котором он прижимается к матрице во время формования при растяжении. Сжатие происходит на противоположной стороне материала от растяжения.
- Морщины: Нежелательные складки, которые могут образовываться на поверхности металла при формовании при растяжении. Сведение к минимуму морщин является ключевой задачей в этом процессе.
- Упругость: тенденция материала частично возвращаться к своей первоначальной форме после растяжения.
- Зажим: Метод закрепления краев металлического листа или детали для предотвращения смещения в процессе формования при растяжении.
- Толщина материала: Толщина металлического листа или детали, используемой при формовании при растяжении.
- Упрочнение при обработке: Процесс, при котором металл становится тверже и менее пластичным при растяжении или изгибе. Для материалов с упрочненной обработкой могут потребоваться различные стратегии формования.
- Формовочный блок: твердый компонент, который поддерживает металлический лист или деталь во время растяжения. Формовочный блок помогает сохранить форму детали и снизить риск образования складок.
- Формовочная смазка: Смазочный материал, наносимый на поверхность металла для уменьшения трения во время растяжения и предотвращения царапин или повреждения материала.
- Гидравлическое растягивающее формование: Процесс растягивающего формования, при котором используется гидравлическое давление для достижения требуемого усилия растяжения.
- Механическое растягивающее формование: Процесс растягивающего формования, в котором используются механические средства, такие как винты или храповики, для приложения необходимого растягивающего усилия.
Механика растягивающего формования
Механика формования при растяжении включает в себя различные физические изменения в зависимости от площади, которые испытывает труба при изгибе. Эти изменения зависят от используемой технологии гибки и свойств материала трубы. Вот ключевые механические аспекты:
- Истончение внешней стенки: При изгибе внешняя сторона трубы подвергается растягивающим усилиям, что приводит к удлинению и истончению стенки.
- Сморщивание внутренней стенки: Внутренняя сторона трубы испытывает сжимающие усилия, приводящие к сморщиванию и утолщению стенки.
- Овальность: Овальность относится к искажению поперечного сечения трубы по сравнению с ее первоначальной круглой формой после изгиба. Это происходит из-за несбалансированных усилий, особенно в неподдерживаемых внутренних частях трубы. Овальность может быть приемлемой в некоторых областях применения, но отрасли со строгими требованиями к размерам должны контролировать ее.
- Коэффициент толщины стенки: Коэффициент толщины стенки представляет собой относительную толщину стенки, рассчитанную как отношение наружного диаметра трубы к толщине ее стенки. Он классифицирует трубы как «толстостенные» или «тонкостенные». Трубы с меньшими коэффициентами толщины стенки легче сгибать, поскольку для них требуется меньшее растяжение материала.
- D изгиба: «D изгиба» — это термин, используемый при изготовлении труб для описания отношения радиуса центральной линии изгиба (CLR) к наружному диаметру трубы. Большее значение D изгиба указывает на более легкую гибку при узких радиусах. Идеальный сценарий для изгибов без опоры предполагает низкий коэффициент стенообразования и высокий D изгиба для предотвращения обрушения внешней стены.
- Относительное удлинение: Относительное удлинение измеряет способность материала растягиваться перед разрывом. Степень изгиба и свойства материала, такие как прочность на растяжение и толщина стенки, влияют на относительное удлинение. Например, нержавеющая сталь имеет более высокий процент относительного удлинения по сравнению с мягкой сталью.
- Возвратная пружина: Возвратная пружина возникает, когда изогнутая труба пытается вернуться к своей первоначальной плоской форме, что приводит к немного меньшему углу изгиба. Чтобы компенсировать это, операторы могут намеренно «перегибать» для достижения желаемого угла изгиба. На возвратную пружину влияют жесткость материала, предел прочности при растяжении, толщина стенки, тип оснастки и техника гибки. Более твердые материалы и меньшие значения CLR приводят к более значительному возврату пружины.
Как работает растягивающее формование?
Растягивающее формование — это процесс, при котором используется гидравлический или механический пресс для растягивания металлического листа или экструзии через матрицу. Матрица, изготовленная из твердого материала, такого как сталь или алюминий, имеет форму, обратную желаемому готовому изделию. Затем металлический лист плотно зажимается вокруг матрицы с помощью захватов, и пресс прикладывает давление, чтобы растянуть лист, придавая ему форму матрицы.

- Подготовка материала: Процесс начинается с листа металла или другого материала, которому часто предварительно придается желаемая форма. Толщина и тип материала зависят от конкретного применения и требований к деталям.
- Зажим и фиксация: Лист надежно зажимается и удерживается на месте с помощью набора штампов или пресс-форм. Эти штампы предназначены для придания материалу желаемой формы при приложении давления.
- Растяжение и сжатие: Формование при растяжении включает в себя как растягивающие, так и сжимающие усилия. Растягивающее усилие прикладывается к листу в тех областях, где требуется удлинение, в то время как сжимающие усилия прикладываются к областям, которые необходимо уплотнить.
- Гидравлическое или механическое давление: Гидравлические или механические системы прикладывают контролируемое давление для растяжения и деформации материала. Это давление точно регулируется для достижения желаемой формы, не вызывая чрезмерного истончения или образования складок.
- Постепенное формование: Процесс формования, как правило, постепенный, при этом материал постепенно растягивается или сжимается до тех пор, пока он не примет форму штампов.
- Контроль качества: На протяжении всего процесса применяются меры контроля качества, такие как контроль толщины материала и точности формы, чтобы гарантировать соответствие формованной детали требуемым техническим требованиям.
Хозяин машины для формирования трехмерных Растяжек
Основная рама оборудования для трехмерной гибки состоит из сварной каркасной конструкции корпуса, установленной на фундаменте:
- Основная рама используется для поддержки поворотного растягивающего коромысла 2 и гидроцилиндра. В верхней части рамы установлена рабочая платформа для размещения пресс-форм.
- Два кронштейна для растягивающих цилиндров установлены соответственно на верхней части рычага коромысла и приводятся в электрическое положение с помощью спиральной направляющей штанги с электроприводом для адаптации к заготовкам различной длины. Каждый рычаг коромысла оснащен натяжным цилиндром.
- Скручивание детали осуществляется гидромотором с редуктором, установленным за растягивающим цилиндром.
- Растягивающий цилиндр установлен на кронштейне с помощью универсального шарнира, который позволяет зажимным губкам свободно вращаться вперед или назад.
- Цилиндр подъема зажима обеспечивает постепенный подъем растягивающего цилиндра в процессе растяжения. Цилиндр наклона зажима может заставлять растягивающий цилиндр наклоняться вверх и вниз. Все действия кинематической пары на кронштейн (растяжение-подъем-наклон-вращение) создают заготовку В течение всего процесса формования, трехмерная поверхность пресс-формы подвергается тангенциальному растяжению для формирования трехмерной заготовки.
Структура оборудования и принцип работы оборудования
Ключевой технологией 3D-гибки является, главным образом, проектирование пресс-формы. 3D-гибочный станок не даст идеальной программы 3D-гибки. Разработчикам технологических процессов необходимо проводить систематический анализ или анализ методом конечных элементов CAE, основанный на свойствах материала и гибочной обработке, а непрерывное пробное производство заготовок требует от технических специалистов-технологов высоких возможностей в области исследований и разработок продукции для достижения наилучшего соответствия между трехмерной гибочной формой и программой трехмерной гибки и удовлетворения технические требования к обрабатываемой детали.
Пространственные трехмерные заготовки находят множество применений в конструкциях передних частей высокоскоростных поездов и производстве самолетов. Продукция отличается высоким техническим содержанием, высокими инвестиционными затратами на изготовление пресс-форм, длительными циклами исследований и разработок и высокой добавленной стоимостью продукции.
Материалы, используемые при формовании методом растяжения
Процесс растягивающего формования обычно используется при изгибе алюминиевых листов, экструдированных профилей, нержавеющих листов, гнутых или рулонных профилей, конструкционных профилей, различных стальных сплавов, латуни, бронзы, меди, титана и даже инконеля. Он позволяет изгибать контуры истинного радиуса, эллипсы, сложные изгибы и спиральные изгибы и может включать прямые ножки.
Стретч-формование можно использовать с различными материалами, включая алюминий, сталь и титан. Эти материалы часто используются в таких отраслях, как аэрокосмическая промышленность, автомобилестроение и строительство, благодаря их высокому соотношению прочности к весу и долговечности.
Вот некоторые из материалов, которые можно использовать при стретч-формовании:
- Алюминий: Алюминий — это легкий и устойчивый к коррозии материал, который обычно используется в аэрокосмической промышленности и автомобилестроении.
- Сталь: Сталь — это прочный материал с высокой прочностью на растяжение. Он широко используется в строительной промышленности для таких применений, как строительство мостов и каркасов зданий.
- Титан: Титан — это легкий и высокопрочный материал, который широко используется в аэрокосмической промышленности. Он обладает отличной коррозионной стойкостью и выдерживает высокие температуры.
Каковы четыре метода формирования растяжки?
- Формовка с растягиванием: При этом методе плоский лист металла зажимается по краям, а затем натягивается на форму или штамп, который растягивает металл до желаемой формы.
- Растягивающее обертывание, также называемое ротационным растягивающим формованием: При этом методе металлическую трубку или экструзию оборачивают вокруг формы или оправки, а затем натягивают или прокатывают по ряду роликов, чтобы растянуть материал до желаемой формы.
- Прессование: При этом методе металлический лист зажимается между двумя штампами, а затем сжимается для придания желаемой формы. Этот процесс может выполняться как горячим, так и холодным способом, в зависимости от материала.
- Формовка радиальной вытяжкой: При этом методе плоский лист металла зажимается по краям, а затем вытягивается в форму или матрицу с помощью пуансона. Металл растягивается и ему придается желаемая форма по мере его втягивания в матрицу.
Принципы проектирования кривизны для растягиваемых формовочных заготовок
Каковы различные типы формования при растяжении?
Продольные и поперечные — это два основных типа формовочных машин для растяжки. Формовочные машины для продольной растяжки растягивают заготовку по ее длине, в то время как формовочные машины для поперечной растяжки растягивают заготовку по ее ширине.
В обоих типах формовочных машин для растяжения губки или захваты удерживают и растягивают металлический лист или экструзию, пока он формируется на столе штампа. Стол штампа обеспечивает форму для растягиваемого металла, а гидравлическая система обеспечивает усилие, необходимое для управления процессом растяжения.
Два типа приложений
Процесс формования листа при растяжении
Формовка листового проката - это производственный процесс, используемый для придания листовому металлу сложных трехмерных форм. Он включает в себя растягивание листа металла на матрице, в результате чего он деформируется и принимает форму матрицы.
Листовая формовка на растяжку обычно используется авиастроителями для изготовления секций обшивки фюзеляжа из специальных листов аэрокосмического алюминиевого сплава. Во время процесса формования металла с растяжением (также известного как «формование намоткой»), при котором лист металла оборачивается вокруг оправки или формы, используя натяжение для создания трехмерной формы. Растягивающее формование (wrap forming) обычно включает в себя обертывание металла поверх формы и последующее вдавливание металла в форму с помощью механического или гидравлического пресса. Этот процесс обычно используется в аэрокосмической промышленности для создания сложных изогнутых или контурных деталей для самолетов и космических аппаратов.
Процесс обычно начинается с плоского листа металла, который зажимается по краям и удерживается на месте. Затем лист растягивают и деформируют, прикладывая контролируемые усилия или давление. Это растяжение приводит к истончению металла в одних областях и растяжению в других, что позволяет ему соответствовать форме штампа.
Какие металлы можно использовать для процесса формования листов при растяжении
- Этому методу можно придать форму любому пластичному металлу.
- Процесс в основном применяется к алюминиевым сплавам для обшивки самолетов.
- Магниевые сплавы формуются при растяжении в горячем состоянии.
- Нержавеющая сталь и титан формуются при растяжении в промышленных масштабах.
- Процессам присущи утончение и деформационное упрочнение. Важно знать значения относительного удлинения для используемого металла. Лучше всего использовать большие значения относительного удлинения. Уменьшение толщины не должно превышать 5% от первоначальной толщины.
Процесс экструзионного растягивающего формования
Конструкции экструзионных прессов для формования профилей из алюминиевых аэрокосмических сплавов для придания формы профилям, сформованным экструзионным способом, или профилям с заторможенным прессованием. Эти профильные прессы для формования иногда называют прессами для растягивания или прессами с поворотными рычагами. Базовая конструкция пресса имеет два рычага или каретки, которые удерживают многопозиционные захватные губки. Зажимы прикреплены к гидравлическим натяжным цилиндрам, которые обеспечивают растяжение заготовки. Рычаги качаются, вращаясь на больших обработанных штифтах с подшипниками, что позволяет заготовке обхватывать формовочную матрицу и прижиматься к ней.
В чем разница между формованием при растяжении и изгибом?
При формовании с растяжением материал зажимается по краям и натягивается на форму или матрицу, что приводит к истончению материала и растягиванию в направлении силы растяжения. Это может привести к более гладкой отделке поверхности и более жестким допускам, особенно для сложных форм или деталей с большими радиусами.
При изгибе к материалу прикладывается усилие для создания желаемого угла или формы. Материал не растягивается, а вместо этого подвергается сжатию по внутреннему радиусу изгиба и растяжению по внешнему радиусу. Минимальный радиус изгиба при гибке обычно меньше, чем при растяжении, и этот процесс может быть использован для более широкого спектра материалов и геометрий.
- Технологический процесс: В процессе формования с растяжением металлический лист или полосу зажимают по краям, а затем натягивают на матрицу или форму. Этот процесс может быть выполнен за один проход или несколько проходов. Напротив, гибка предполагает приложение усилия к металлическому листу или трубе для создания желаемого угла или формы.
- Материал: Формование растяжением обычно используется для более пластичных материалов, таких как алюминий, в то время как гибка может применяться для более широкого спектра материалов, включая сталь, нержавеющую сталь и алюминий.
- Сложность: Растягивающая формовка часто используется для получения более сложных форм и изгибов, в то время как гибка лучше подходит для более простых геометрий и углов.
- Точность: Растягивающая формовка известна своей высокой точностью, что делает ее идеальной для аэрокосмической и автомобильной промышленности, где требуются жесткие допуски. С другой стороны, изгиб может привести к большим различиям в конечном продукте из-за таких факторов, как упругость и толщина материала
Применение растяжения
Почти любую форму, которую можно получить другими методами формовки листового материала, можно получить с использованием метода растяжения.
Растяжение применяется для формовки деталей для авиакосмической промышленности из сталей, никеля, алюминия, титановых сплавов и других термостойких и огнеупорных металлов. Некоторые из этих деталей трудно или невозможно формовать другими методами, например, кольцо газотурбинного титанового сплава.
Также растяжение применяется для формовки деталей автомобильных кузовов, как внутренних, так и внешних, а также элементов рамы, которые могли бы быть сформированы другими методами, но по более высокой стоимости.
Для чего используется растяжение?
Типичными деталями, формуемыми при растяжении, являются большие изогнутые панели, такие как дверные панели в автомобилях или панели крыльев самолетов. Разнообразие форм и поперечных сечений, которые можно растягивать и формировать, практически неограниченно. Оконные системы, мансардные окна, витрины магазинов, вывески, мигалки, навесные стены, ограждения для пешеходных дорожек и поручни могут быть точно сформированы в соответствии с желаемыми профилями.. Другие детали, формованные растяжением, можно найти в оконных рамах и ограждениях. Строгие и согласованные допуски, отсутствие дефектов поверхности, искажений или ряби, а также несоосность поверхности сложных профилей являются важными преимуществами, присущими формованию при растяжении. Гладкая и ровная поверхность получается в результате процесса формования при растяжении. Этот процесс идеально подходит для изготовления крупногабаритных деталей из алюминия, но также хорошо работает с нержавеющей сталью и коммерчески чистым титаном. Он быстрый, эффективный и обладает высокой степенью повторяемости.
Читать далее:
- 4 Шага процесса растяжения
- Измерение арочных отверстий для металла, полученного
Резюме
Растяжение предлагает несколько преимуществ по сравнению с другими методами формовки. Оно позволяет производить крупные изогнутые компоненты с высокой точностью и повторяемостью. Оно также минимизирует утончение материала и поддерживает структурную целостность металла, что приводит к компонентам с отличными соотношениями прочности и массы. Кроме того, растяжение исключает необходимость в нескольких операциях формовки, сокращая время и затраты производства.
В целом растяжение является универсальным и эффективным процессом для формовки листового материала и экструзий в сложные изогнутые компоненты, что делает его ценным методом в различных отраслях промышленности.