Гидравлический пресс станок Производитель
Гидравлический пресс
Диапазон мощности оф 10T to 15000T, Гидравлические прессы для любого применения
Базовые знания гидравлического пресса.
Что такое гидравлический пресс?
Гидравлический пресс — это машина, использующая жидкость в качестве рабочего тела и созданная по принципу Паскаля для передачи энергии для реализации различных процессов. Гидравлический пресс обычно состоит из трех частей: машины (хозяина), системы питания и системы гидравлического управления.
Применение гидравлического пресса
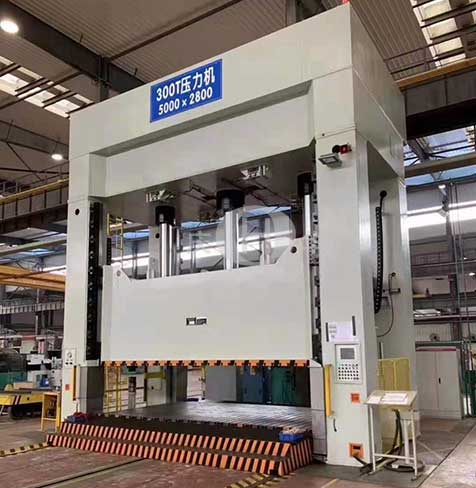
Гидравлические прессы используют гидростатическое давление для обработки металла, пластика, резины, дерева, порошка и других продуктов и часто используются в процессах прессования и прессования, таких как ковка, штамповка, холодная экструзия, правка, гибка (например, листогибочные машины, Гибочные станки)), отбортовки, волочения листов, порошковой металлургии, пресс-фитинга и т. д. Помимо ковки и формовки, гидравлические прессы также могут использоваться для правки, прессования, упаковки, прессования блоков, прессования плит.
Принцип работы и классификация гидравлического пресса
Основной гидравлический пресс — это машина, созданная по закону Паскаля и использующая передачу гидравлического давления, и существует множество типов. Конечно, использование также варьируется в зависимости от потребностей. Например, по типу жидкости, передающей давление, различают водяные гидравлические прессы и масляные гидравлические прессы.
Жидкость на водной основе в качестве рабочей среды также называют водным гидравлическим прессом, а масло в качестве рабочей среды также называют масляным гидравлическим прессом.
Общее давление, создаваемое водным гидравлическим прессом, велико и часто используется при ковке и штамповке. Гидравлический пресс для ковки делится на гидравлический пресс для штамповки и гидравлический пресс для свободной ковки. В гидравлических прессах для штамповки используются формы, а в гидравлических прессах для свободной ковки формы не используются.
Технические характеристики гидравлических прессов обычно выражаются в номинальной рабочей силе (kN) или номинальном тоннаже (tons).
Ковочные гидравлические прессы в основном представляют собой гидравлические прессы на водной основе с большой грузоподъемностью. В больших ковочных гидравлических прессах с целью уменьшения габаритов оборудования часто применяют более высокие давления (около 35 МПа), а иногда применяют и сверхвысокие давления, превышающие 100 МПа. Гидравлические прессы для других целей обычно используют рабочее давление от 6 до 25 МПа.
Тоннаж гидравлического пресса на масляной основе ниже, чем у гидравлического пресса на водной основе.
Протирочная Работа Гидравлического Пресса
Принцип Паскаля
Принцип работы гидравлического пресса. Площади большого и малого плунжеров равны S2 и S1 соответственно, а силы, действующие на плунжеры, равны F2 и F1 соответственно. Согласно принципу Паскаля, давление замкнутой жидкости везде одинаково, т. е. F2/S2=F1/S1=p; Ф2=Ф1(С2/С1). Указывает гидравлическое усиление. Как и при механическом выигрыше, сила увеличивается, но работа не увеличивается. Следовательно, расстояние перемещения большого плунжера в S1/S2 раз превышает расстояние перемещения маленького плунжера.
Фундаментальный
Основной принцип заключается в том, что масляный насос подает гидравлическое масло во встроенный блок картриджных клапанов и распределяет гидравлическое масло в верхнюю или нижнюю полость цилиндра через каждый односторонний клапан и предохранительный клапан, а также заставляет цилиндр двигаться под давлением. действие масла высокого давления.
Жидкости подчиняются закону Паскаля, когда они передают давление в закрытом сосуде.
Протирание середины гидравлического пресса
Функция рабочей среды, используемой в гидравлическом прессе, заключается не только в передаче давления, но и в обеспечении чувствительности, надежности, долговечности и меньшей протечек рабочих частей машины.
5 основные требования гидравлического пресса к рабочей жидкости
- Иметь подходящую текучесть и низкую сжимаемость для повышения эффективности передачи;
- Может предотвратить ржавчину;
- Иметь хорошие смазочные характеристики;
- Легко запечатывать;
- Стабильная производительность, длительная работа без ухудшения качества.
Три рабочих тела гидравлического пресса
- Гидравлический пресс первоначально использовал воду в качестве рабочей среды, а позже перешел на эмульсию, приготовленную путем добавления в воду небольшого количества эмульгированного масла для повышения смазывающей способности и уменьшения ржавчины.
- В конце 19 века появились гидравлические прессы, использующие в качестве рабочего тела минеральное масло. Масло обладает хорошей смазывающей способностью, устойчивостью к коррозии и умеренной вязкостью, что способствует повышению производительности гидравлических прессов.
- Во второй половине XX века появился новый тип эмульсии на водной основе, форма его эмульгирования была «вода в масле» вместо первоначальной «масло в воде».
Внешняя фаза эмульсии «вода в масле» представляет собой масло, его смазочные и антикоррозионные свойства близки к маслу, содержание масла в нем очень мало, и его нелегко сжечь. Однако эмульсия на водной основе стоит дорого, что ограничивает ее продвижение.
Конструкция гидравлического пресса
Система привода
Система привода гидравлического пресса в основном имеет два типа прямого привода насоса и привода насоса-аккумулятора.
Насос с прямым приводом
Насос этой системы привода подает рабочую жидкость под высоким давлением в гидроцилиндр, распределительный клапан используется для изменения направления подачи жидкости, а предохранительный клапан — для регулировки ограниченного давления системы, и в то же время играют роль предохранительного устройства.
Система прямого привода насоса имеет мало звеньев и простую конструкцию. Давление можно автоматически увеличивать или уменьшать в зависимости от требуемой рабочей силы, что снижает энергопотребление. Однако мощность насоса и его приводного двигателя должна определяться максимальной рабочей силой и максимальной рабочей скоростью гидравлического пресса.
Этот тип системы привода в основном используется в гидравлических прессах малого и среднего размера, а также в крупногабаритных (например, 120 000 кН) гидравлических прессах свободной ковки с прямым приводом от насосов.
Насосно-аккумуляторный привод
В системе привода насос-аккумулятор имеется один или группа аккумуляторов.
При избытке рабочей жидкости высокого давления, подаваемой насосом, она накапливается в гидроаккумуляторе;
А когда запаса не хватит, его дополнит аккумулятор.
В этой системе мощность насоса и двигателя можно выбрать в соответствии со средним расходом рабочей жидкости высокого давления, но поскольку давление рабочей жидкости постоянно, потребляемая мощность велика, и система имеет много связей. и сложная структура.
Система привода насос-аккумулятор чаще всего используется для больших гидравлических прессов или комплект приводной системы приводит в движение несколько гидравлических прессов.
Тип структуры
Вертикальное и горизонтальное
Гидравлические прессы классифицируются по направлению силы. Существует два типа гидравлических прессов: вертикальные и горизонтальные. Большинство гидравлических прессов являются вертикальными, а гидравлические прессы для экструзии преимущественно горизонтальными.
Тип структуры
Гидравлические прессы включают двухколонную, четырехколонную, восьмиколонную, сварную раму и многослойную намоточную раму из стальной ленты, а средние и малые вертикальные гидравлические прессы также используют C-образную раму.
- Гидравлический пресс с C-образной рамой открыт с трех сторон, он прост в эксплуатации, но имеет низкую жесткость.
- Прессы гидравлические для штамповки сварной рамы имеют хорошую жесткость, открыты спереди и сзади, но закрыты слева и справа.
- В вертикальном четырехколонном гидравлическом прессе свободной ковки с верхней передачей масляный цилиндр закреплен в верхней балке, плунжер жестко связан с подвижной балкой, а подвижная балка направляется колонной и перемещается вверх и вниз под давление рабочей жидкости. На балке находится рабочий стол, который может перемещаться вперед и назад. Верхняя и нижняя наковальни установлены соответственно под подвижной балкой и на рабочем столе. Рабочая сила воспринимается рамой, состоящей из верхних и нижних балок и колонн.
- Большие и средние гидравлические прессы свободной ковки с приводом от насоса-аккумулятора часто используют три рабочих цилиндра для получения трехуровневой рабочей силы. За пределами рабочего цилиндра также расположены балансировочные цилиндры и возвратные цилиндры, которые создают восходящую силу.
Четырехколонный гидравлический пресс
Четырехколонный гидравлический пресс подходит для прессования пластмассовых материалов. Такие как формование порошковых изделий, формование пластиковых изделий, формование металла холодной (горячей) экструзией, растяжение листов и такие процессы, как поперечное прессование, гибка, проворачивание и коррекция.
Четырехколонный гидравлический пресс можно разделить на четырехколонный двухбалочный гидравлический пресс, четырехколонный трехбалочный гидравлический пресс, четырехколонный четырехбалочный гидравлический пресс и т. д.
Гидравлический пресс с одним рычагом (Гидравлический пресс с одной колонной)
Рабочий диапазон можно расширить, а трехстороннее пространство можно использовать для удлинения хода гидравлического цилиндра (опционально), максимальный выдвижной 260–800 мм, а рабочее давление можно предварительно настроить; Устройство охлаждения гидросистемы.
Портальный гидравлический пресс
Портальный гидравлический пресс может выполнять сборку, разборку, выпрямление, каландрирование, растяжение, гибку, штамповку и другие работы с деталями машин, что делает машину действительно многоцелевой. Рабочий стол портального гидравлического пресса может перемещаться вверх и вниз, размер увеличивает высоту открытия и закрытия машины, и его удобнее использовать.
Двухколонный гидравлический пресс
Серия двухколонных гидравлических прессов подходит для запрессовки, гибки и формовки, тиснения и вдавливания, отбортовки, штамповки и мелкого растяжения мелких деталей различных деталей; формование изделий из металлического порошка и другие процессы обработки.
Двухколонный гидравлический пресс оснащен электрическим управлением, оснащен толчком и полуавтоматической циркуляцией, может поддерживать давление и задержку, имеет хорошее управление ползунком, удобное управление, простоту обслуживания, экономичный и долговечный. В соответствии с потребностями пользователей могут быть добавлены такие функции, как термический прибор, цилиндр эжектора, цифровое отображение хода и подсчет.
Приложение
Детали с центральной нагрузкой
Гидравлический пресс особенно подходит для гибки, формовки, маркировки и других процессов деталей с центральной нагрузкой. Буферное устройство для перфорации, его также можно использовать для обработки штамповки и вырубки. Предпочтительный продукт.
Детали из листового металла
Гидравлический пресс используется для процессов волочения, галтовки, гибки и штамповки деталей из листового металла, а также может использоваться для общих процессов прессования. В соответствии с потребностями пользователя могут быть добавлены такие устройства, как буферы для перфорации, перфораторы и подвижные рабочие столы.
Процесс прессования
Гидравлический пресс также может использоваться для процесса прессования деталей вала, калибровки, обжима и прессования профилей, а также процессов гибки, распиливания, формования, тиснения, формования гильз, вытягивания и прессования пластмассовых материалов листовых деталей. Такие операции, как штамповка, гибка, отбортовка, тонкая вытяжка и другие операции, также могут выполняться при калибровке, запрессовке, прессовании и формовании пластиковых изделий и порошковых изделий. Его еще называют универсальным гидравлическим прессом из-за широкого спектра применения.
Другой
Помимо ковки и формовки, трехлучевой четырехколонный гидравлический пресс также может использоваться для правки, прессования, упаковки, прессования блоков и прессования плит.
Преимущества гидравлических прессов
По сравнению с традиционным процессом штамповки процесс гидроформовки имеет очевидные технические и экономические преимущества в снижении веса, уменьшении количества деталей и форм, повышении жесткости и прочности, а также снижении производственных затрат и широко используется в промышленной сфере, особенно в первую очередь в автомобильной промышленности. все больше и больше приложений.
Методы гидроформинга
В автомобильной, авиационной, аэрокосмической и других областях снижение массы конструкции для экономии энергии во время эксплуатации является долгосрочной целью, которую преследуют люди, а также одной из тенденций развития передовых технологий производства. Гидроформинг – это передовая технология производства, позволяющая создавать легкие конструкции.
Гидроформинг также известен как «внутренняя формовка под высоким давлением». Его основной принцип заключается в использовании трубы в качестве заготовки, подаче внутрь трубы жидкости сверхвысокого давления и приложении осевого усилия к обоим концам заготовки трубы для пополнения материала. Под совместным действием двух внешних сил материал заготовки трубы подвергается пластической деформации и, наконец, прилипает к внутренней стенке полости формы, образуя полую деталь, форма и точность которой соответствуют техническим требованиям.
5 преимуществ технологии гидроформинга
Для полых конструктивных деталей переменного сечения применяется традиционный
Производственный процесс заключается в том, чтобы сначала штамповать и формовать две половинки, а затем сваривать их в одно целое, а гидроформовка позволяет целиком формировать полые детали конструкции, изменяющиеся по поперечному сечению детали.
По сравнению с процессами штамповки и сварки методы и процессы гидроформовки имеют следующие основные преимущества:
- Уменьшите массу и сэкономьте материал. Для типичных деталей, таких как кронштейны автомобильного двигателя и кронштейны радиатора, детали, полученные методом гидроформовки, на 20–40 % легче штампованных деталей; для полых ступенчатых деталей вала вес можно уменьшить на 40–50%.
- Уменьшите количество деталей и форм и уменьшите затраты на пресс-формы. Для деталей гидроформовки обычно требуется только один комплект штампов, тогда как для штампованных деталей чаще всего требуется несколько комплектов штампов. Количество гидроформованных деталей кронштейнов двигателя уменьшено с 6 до 1, а количество деталей кронштейнов радиатора уменьшено с 17 до 10.
- Это может уменьшить количество сварки для последующей обработки и сборки. На примере кронштейна радиатора площадь рассеивания тепла увеличена на 43%, количество паяных соединений уменьшено со 174 до 20, количество процессов уменьшено с 13 до 6, производительность увеличена на 66%.
- Улучшите прочность и жесткость, особенно усталостную прочность. Например, жесткость гидроформованного кронштейна радиатора можно увеличить на 39% в вертикальном направлении и на 50% в горизонтальном.
- Сократить производственные затраты. Согласно статистическому анализу применяемых гидроформованных деталей, себестоимость изготовления гидроформованных деталей в среднем на 15–20 % ниже, чем у штампованных деталей, а стоимость пресс-формы снижается на 20–30 %.